Lane’s legacy – Co-op to remain in growers’ hands
More than $50 million in capital upgrades, including an expansion into New South Wales and the addition of a value-adding plant in Renmark, are some of the highlights from Simon Lane’s tenure as chairman of the Almondco Australia board.
Mr Lane stepped aside in March 2020 after nearly eight years at the helm, coinciding with the adoption of the new company constitution, another of his major projects with the co-operative.
He vacated the position with Almondco arguably in its strongest ever position but the fact he had little agricultural experience compared to a majority of board members underlines what he felt was an important lesson for all companies and cooperatives alike.
Almondco’s board structure includes four grower directors, two independent directors and a managing director.
“I believe one of the keys to the success of Almondco is that it has two independent directors, who don’t own an almond tree, or own a share in the company,” Mr Lane explained.
“In my opinion, it is the best structure there is for a co-op.
“Many a co-operative has fallen by the wayside because it had the skills of its farmer directors but didn’t have the people from different backgrounds that are relevant to a well-run company.
“Another reason the Almondco board is so successful and strong is the grower directors all have a real commitment to the company that transcends their personal interest.
“They invariably talk of what’s in the best interest of growers as a whole, not their own self-interest.”
Mr Lane has a background in the legal industry.
He started working with the newly established consumer affairs branch in the early 1970s and later that decade, he moved across to the Corporate Affairs Commission (CAC), a state-based precursor to what would later be known as the Australian Securities and Investments Commission (ASIC), which included regulating co-ops, investigating and prosecuting corporate fraud.
Mr Lane joined the independent bar as a barrister in 1989 and continued there until 2006.
Three years earlier, he established a mediation practice, which he still runs today.
His links to Almondco were formed in 2012 after being approached by board member and grower, Andrew Lacey, following a recommendation from a mutual business connection.
“He had heard of my background and felt the skills I had were what Almondco needed at the time,” Mr Lane said.
The company had some issues that needed attention, which required a legal focus.
“I’d like to think in the nearly eight years I was there that I was able to tidy a few of those things up,” Mr Lane said.
The approach sparked instant curiosity.
“I was interested in the fact it was a co-op, partly through my time with the CAC but also philosophically, I’ve always had a strong attachment to co-ops as an agricultural business model,” Mr Lane said.
“I think they are the only way farmers, be they big or small, can ultimately survive.”
Visits to a relative’s dairy farm near Mount Gambier were Mr Lane’s introduction to agriculture and his eventual purchase of a small hobby farm with some cattle, plus olive and timber plantations in Willunga, fuelled a connection with the land.
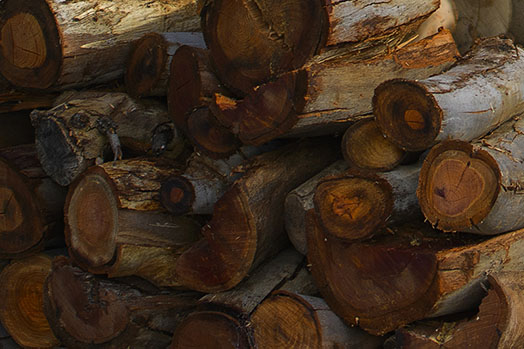

Still, with a vast majority of his professional career spent in legal circles, there was the possibility his lack of agricultural experience could have been a sticking point with fellow Almondco board members.
“I didn’t sense any hostility at all,” Mr Lane said.
In fact, his different perspective on issues, along with that of fellow independent board member, Russell Witcombe, highlighted the reasoning behind their appointments.
Mr Lane’s legal nous, including matters of corporate governance and risk mitigation, coupled with Mr Witcombe’s economic and business understanding, helped contribute to the board making some major improvements.
“In my experience, it is often knowing the right questions to ask, and in addition to not be frightened to ask what might appear to be ‘silly questions’, because sometimes the silly questions are asking something no one has really thought about before,” Mr Lane said.
“When you start exploring it, it can throw up some quite useful information.”
Mr Witcombe continually probed the concept of how Almondco could dry wet product, long believed by industry insiders to be a brick wall.
“All the grower directors on the board knew there was no effective way of drying wet almonds,” Mr Lane said.
“But he kept persisting with it as a wet harvest could be seriously detrimental to the business.”
Eventually, Almondco management found a new drying system set up in the Riverina region, which had real potential.
“Russell’s independent questioning had ultimately produced a partial or substantial answer to a problem growers, up until that time, had said was an unanswerable question,” Mr Lane said.
Mr Lane’s internal governance and risk mitigation focus also proved crucial in major investment decisions, including identifying potential issues following the purchase of the primary processing plant at Lyrup in February 2012, and the installation of the pasteuriser at Renmark at about the same time.
The new primary processing facility redrew the scope of Almondco’s business and became one of the reasons behind the development of a new company constitution.
“It principally needed doing because the company was now a primary and secondary processor,” Mr Lane explained.
Another major purpose of the constitution changes was to enhance Almondco growers’ capacity to retain the company in the hands of its producer members.
“I’ve seen what happens to co-ops when short term self interest prevails over the long term and wider interest of the growers,” Mr Lane said.
“This constitution enabled the growers, if they wanted to, to have an effective way of keeping control of their company so it could remain something that worked for the benefit of all growers, all treated consistently across the board.
“The destiny will largely be in their hands rather than the hands of others, preserving the company as their co-op.
“I think the end product is a pretty good one, time will tell if we’ve achieved that.”
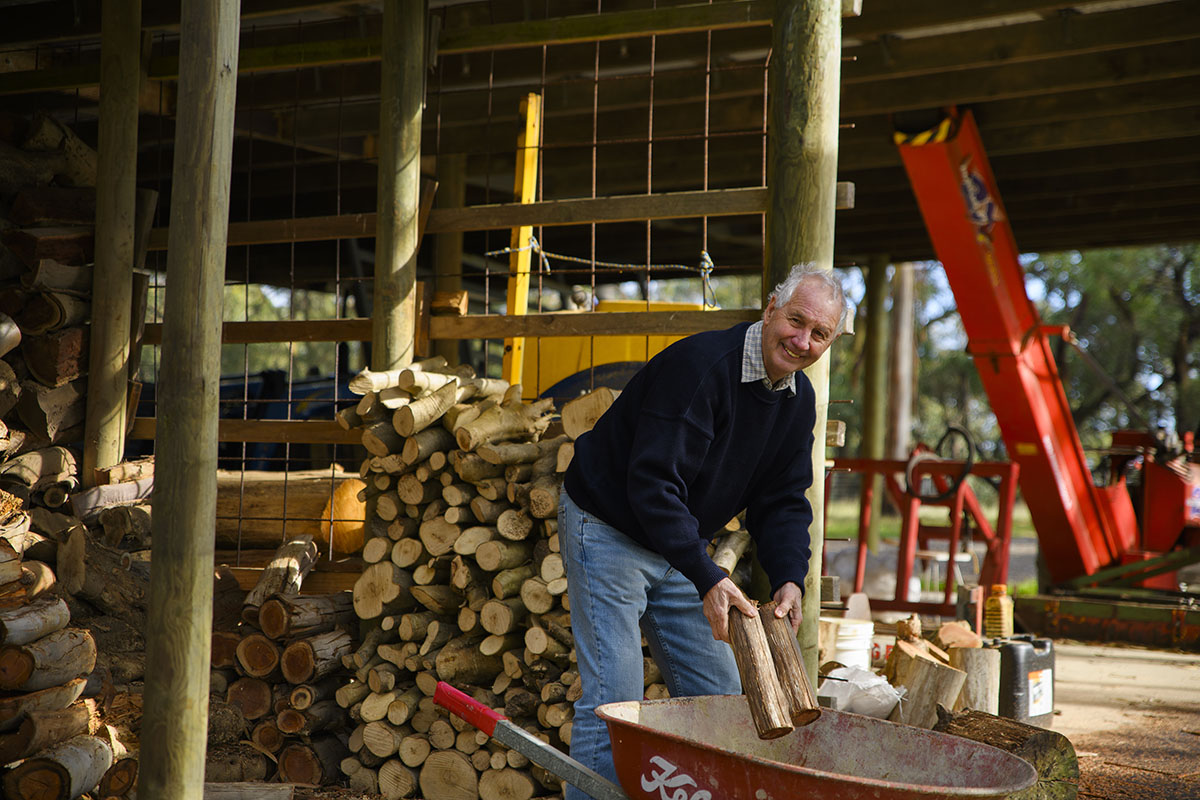
Almondco’s expansion into the Riverina region of New South Wales also had a risk mitigation component.
Within weeks of his appointment, Mr Lane quizzed CEO, Brenton Woolston, on what he thought was the biggest risk Almondco faced.
“He said to me it was the risk of supply of almond product,” Mr Lane said.
“It was a very perceptive and honest response to my question, and absolutely spot on.
“It drove a lot of our thinking; how do we secure our supply?
“All of the growers in the Riverina were potentially new Almondco growers, some were already but relatively few.
“We had to bring the Riverina growers into the family.”
Of course, the Riverina growers were frustrated with not having a local processing facility.
But on the flip side, Almondco couldn’t build a primary processing facility without the grower support.
“It was a hugely difficult balancing exercise,” Mr Lane said.
“That vicious circle had to be broken.”
Mr Lane and Mr Woolston travelled to the region a number of times over a three-year period, negotiating between the interstate growers and the Almondco board.
In the end, the decision was made to invest $25 million on a primary processing and in-shell facility at Griffith.
“My instincts told me to strongly back Brenton to build it when we did,” Mr Lane said.
“My judgement was we had to do it when we did it, if we left it a year, we may miss out.
“Having made the decision, it was then an absolute nightmare to put in place.”
Constant barrages of rain made the work site a quagmire.
The construction period became an increasingly difficult process but was completed substantially on time and very close to budget.
“It was an extraordinary achievement in very difficult circumstances.
“It’s up and running though, and more trees are going in the ground,” Mr Lane said.
“We sort of bookend the industry at the east and west of the major almond growing areas in Australia, we can move product either way and it gives Almondco enormous flexibility.
“It is a major risk mitigating factor as well as adding significant value to the Almondco business.
“So we’ve got huge new plantings going on in the Riverina and we’re now in the strong negotiating position where we can, in effect, pick and choose who we want as our growers.
“That’s a big turnaround from where we were, grasping for supply.”
With that, one of the company’s most pressing issues was addressed.
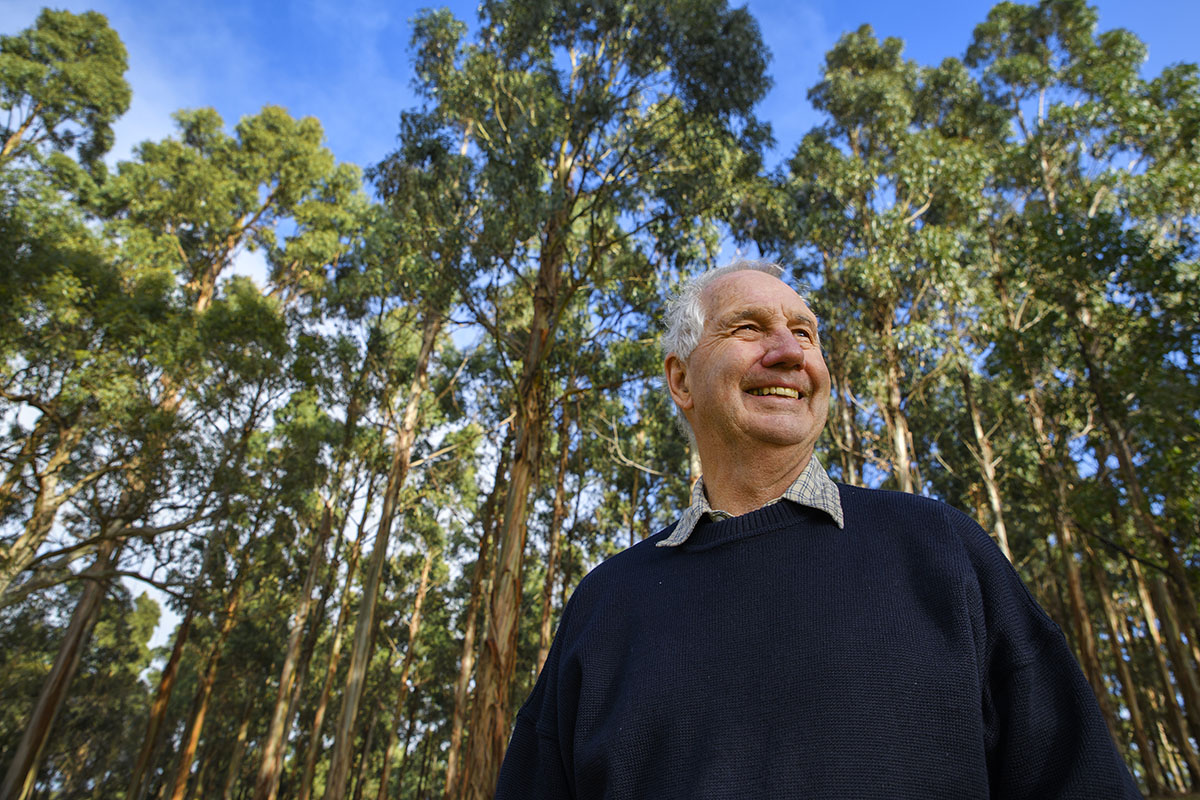
“You should never measure a company just by what it achieves,” Mr Lane said.
“Another significant factor is the extent to which a company avoids problems.
“The best run companies achieve results and don’t have problems, they are smart enough to be ahead of the play and avoid them.
“By and large, in the nearly eight years I was with Almondco, barring very few minor exceptions, we really didn’t have any major problems, and that is also a credit to Brenton, his team and the board.”
The $25 million value-adding expansion at the Renmark site initiated in 2019 also required significant consideration of the risks involved.
Industry talk about three years ago suggested supermarkets were wanting direct access to suppliers, getting as close to the farm gate as possible.
“Part of that discussion included the perception there was an increasing demand for value-added product, particularly blanched almonds,” Mr Lane said.
Almondco had some limited value-adding capacity at the time but that was reliant on old machinery.
Having an increasing range of options with differing standards of product was a tempting prospect.
“With skill and the right equipment, you can add value from the perfect almond, to the worst almond that comes in,” Mr Lane said.
“While growers aspire to produce their best kernel, they can’t always get that, but with this option in place, they would still get something for even the worst quality almond, which happens during primary production.”
From the primary processing plant at Lyrup and the successful commissioning of the new pasteuriser at Renmark, to drafting and adopting the new constitution, trying to strike the right balance between existing growers and new, potentially huge growers, establishing the Riverina facility, developing the range of new primary and secondary processing contracts and finally committing to the value-adding expansion, it has been a busy time in the chair.
“I think, with hindsight, most if not all growers would say all those big ticket items were the right calls to make, that would be my impression,” Mr Lane said.
He formally left the board at the end of March 2020 and plans to spend more time with his family, including a son and grandchildren currently in the USA, while also doing some mentoring work for the Business Council of Co-ops and Mutuals, an umbrella organisation assisting the nation’s co-operatives.
Mr Lane will also continue voluntary work with Stroke SA, a state-based support organisation for stroke victims and their carers.
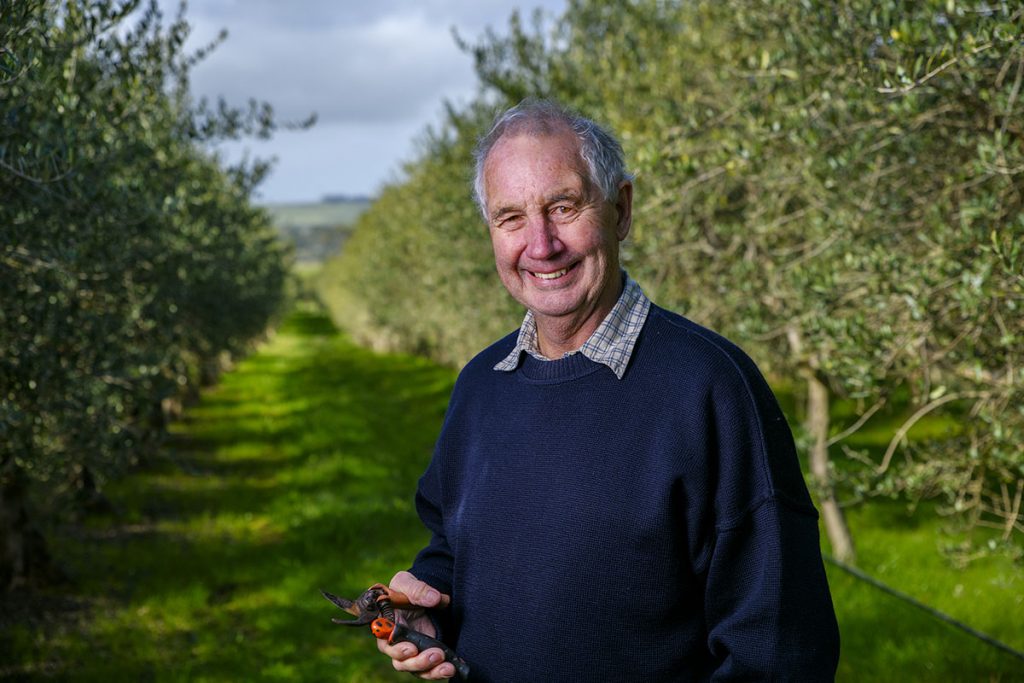
On his departure, he reflected on his time in the chair and where the company stands now.
“There were occasions where we had differences of opinion and perspectives but the whole time I was there, I don’t think we had to put any issue to a vote, we always found a consensus everyone was comfortable with but not always entirely in full agreement,” Mr Lane said.
“You’ll always have different personalities, that’s life, but my clear perception is that with Brenton at the top and the managers below, it’s a strong team with a commitment to the interests of the company and its growers.
“The other key is the establishment and maintenance of relationships within the company, between the company and its various stakeholders and with the diverse range of outside contractors.
“The essence of leadership is to establish those cultures within a company and inculcate them through managers so they permeate throughout the organisation and Brenton deserves a lot of credit for that happening.
“It was already a very good company when I arrived and my goal was to leave it an even better company, and I wish my successor every success in taking it to the next level.
“That’s what leadership is all about, everyone doing their best to try and improve the company.”
While he spent nearly eight years chairing the board of an almond co-op, Mr Lane didn’t leave as an industry expert.
“I didn’t know the difference between carmel and non-pareil when I arrived and I left Almondco still not knowing the difference,” he laughed.
“Part of my thinking with leadership is being able to stand back and see big picture stuff, reinforcing important relationships and not getting too bogged down in detail, other than when strictly necessary.
“Sometimes you have to get into details, but it is crucial knowing when you need to and when you don’t, and make judgments accordingly.”
Mr Lane has his own perspectives on leadership, based on his years of experience.
“I’ve had a view for a very long time that between six and 10 years in any leadership role is about right,” he said.
“It’s good for the individual and good for the organisation to have changes.
“You don’t want to stay too long, you want to get out while people are still happy with you and would want you to stay.
“There is no doubt with any individual in a major leadership role, that responsibility weighs heavily and if you start to sense you’re losing that drive, energy and commitment, that’s the warning sign, when it starts becoming a bit of an effort.”
Despite handing over the reins, Mr Lane’s connections with Almondco still run deep.
“It’s been eight years of my life, I met lots of really nice people, decent human beings, competent employees, and that for me was a tremendous privilege,” he said.
“To this day, I watch the news and still look for the weather in Renmark and Griffith, because rain events have the potential to have a big impact on the business.
“I don’t have any sense after having decided to leave, to wash my hands of it all.
“I hope I can always retain a connection with the company.”
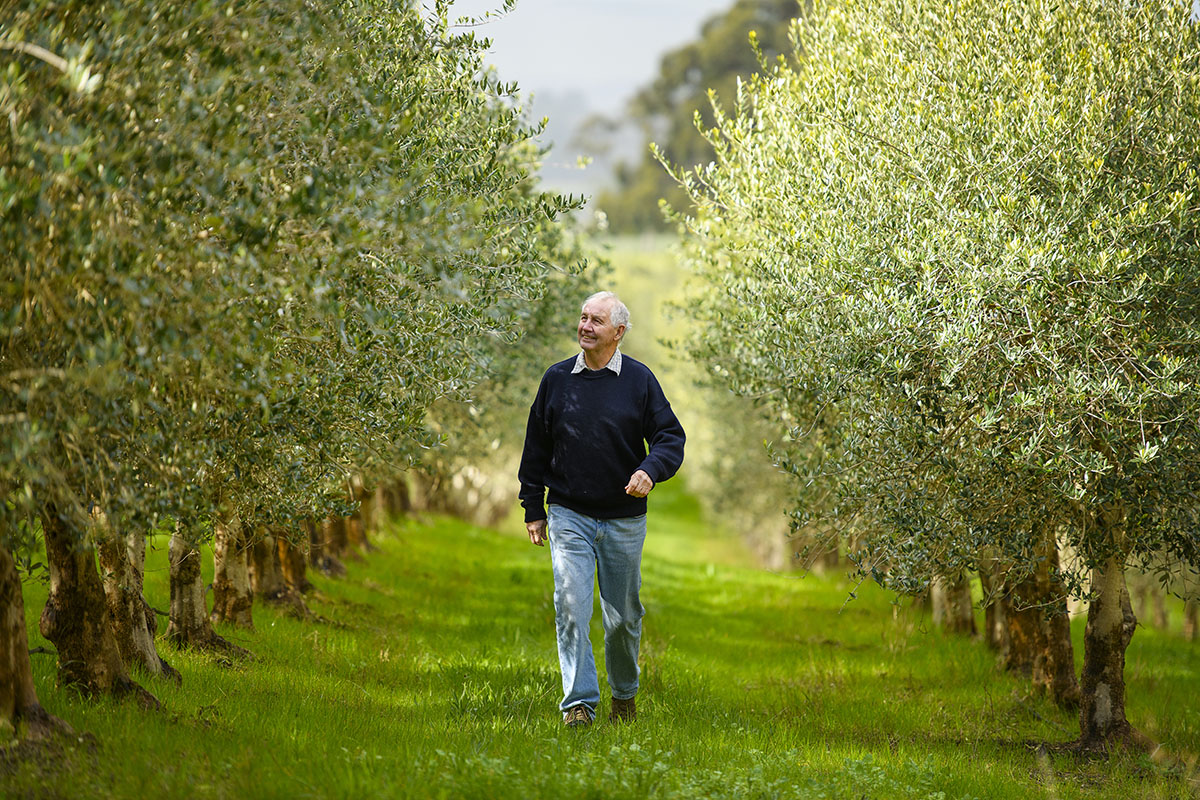
Simone Lane: The Almond Co Story - video transcription
My name is Simon Lane, I was the former Chair of Almondco in South Australia. I want to tell you a really good news story about a co-op that started from very humble beginnings back in the 1940s to now what is an internationally-acclaimed co-op with a turnover of a quarter of a billion dollars a year. It's been an extraordinary journey. I was lucky enough to be involved in it for eight years from 2012-2020. Obviously, an enormous amount of work and thought had gone into the company before I became involved.
Almondco started in very humble beginnings in the outskirts of Adelaide in the 1940s as a true co-op, with every almond grower holding one share. The co-op struggled for many decades and there were a whole range of different pressures. There were constant clashes between growers, with some more focused on self-interest and some on the wider public good. Some didn't have a shared vision. I think it's fair to say with hindsight that the co-op didn't have a particularly long-term vision and it stumbled from decade to decade.
But because it retained some really committed and energetic people throughout that period, it survived. But it wasn't an easy journey. If only the initial co-operators had known then what everyone knows now, I think the journey would have been a lot easier and perhaps a lot more successful.
With an almond, there is an outer hull, then there's the shell and then there's the kernel. The process of removing the hull and the shell is known as primary processing. It's a very dusty and noisy process. Once the kernel is extracted, secondary processing involves the kernel being pasturised, weighed, graded for size and quality, and it's packed and marketed.
In the very early days of the co-op, the hulling and shelling was done using very rudimentary equipment. The supply wasn't constant because from time to time growers would try to pick and choose where they were trying to sell their product. Sometimes they tried to sell their own product separately from the co-op. The co-op remained broadly in that form until the 1990s. At this point, some people with some vision decided that several changes needed to be made. This was brought about, essentially, by the realisation that the suburbs and outskirts of Adelaide were no longer appropriate for almond growing. The price and quality of soil and water became a problem, so many of the growers from the area south of Adelaide moved up to the South Australian Riverland. Huge orchards started to be planted, both by the former Adelaide growers and, increasingly, by people along the Murry in both NSW and Victoria. Now there are almond orchards that cover hundreds and hundreds of hectares.
Against that background, Almondco did two things. Firstly, it closed the plant in Adelaide and it built a secondary processing plant in Renmark. They had the foresight to choose a very large block of land that subsequently they were able to develop. It cost a lot of money, but it turned out to be a very sucessful decision. In terms of primary processing, at that stage Almondco didn't have a primary processing facility: all of the growers, no matter where they were growing, were getting the primary processing done by individual and independent hullers and shellers. There were three or four in the vicinity of the River Murray. In those early days, Almondco was only engaged in secondary processing.
It changed in the 1990s from a pure co-op to a legal structure known as an Unlisted Public Company. Shares were distributed to allotted growers in accordance with the volume of product that they were supplying. Whether that was a good or a bad thing can be debated, but that's what happened. The good news is that the strong co-operative culture was retained and has been retained to this day.
In the period between the early '90s and 2012, all the primary processing (hulling and shelling) was done independently. Almondco did the secondary processing. But in 2012 it bought a primary processing plant from one of the independent operators. From then on, it had full control of the production process. When the growers brought their product in with hull and shell on it, title in those almonds passed to the co-op and all responsibility, including risk, passed to Almondco. They put it through the primary processing plant that they'd bought, they then transported the processed almond kernel across the river to Renmark where it was parturised with a new parturising plant that was installed in 2012. It was then put through the whole secondary processing phase and marketed. These days, Almondco is exporting its product to, I think, 40-odd countries throughout the world and has an international reputation for producing consistently high-quality almonds.
The next stage in its development was as the almond growth extended along the Murray and into the Riverina in NSW. The company built a new, massive processing plant there in 2015. It was a bit of chicken-and-egg because the local growers were saying they wouldn't put almonds in the ground unless the processing plant was put in, and Almondco said in response that it wouldn't make the $25 million expense unless it was sure there would be product coming through the system. We worked our way through all of that and in 2015 we opened and commissions a major new processing plant in the Riverina that has the capacity to be expanded as the number of almonds going into the ground increases.
The company has now, therefore, got two primary processing plants. It has a turnover of approximately $250 million per year and is employing around 170 people. It is now a fully vertically-integrated business.
One of the things that I did just before I retired in March 2020 was to put through an amended constitution. That was very much designed to enhance and maximise the extent to which the growers could retain control of their business. The message that I was met with when I joined Almondco was, "This company exists for its growers." When I left the company eight years later, I hoped that I had been able to enhance that culture by enabling the growers, be they large, medium or small, to all be treated consistently, all have pride in their company, and all get the benefits, individually, of their joint co-operation, with very co-operatively minded management and board of directors.
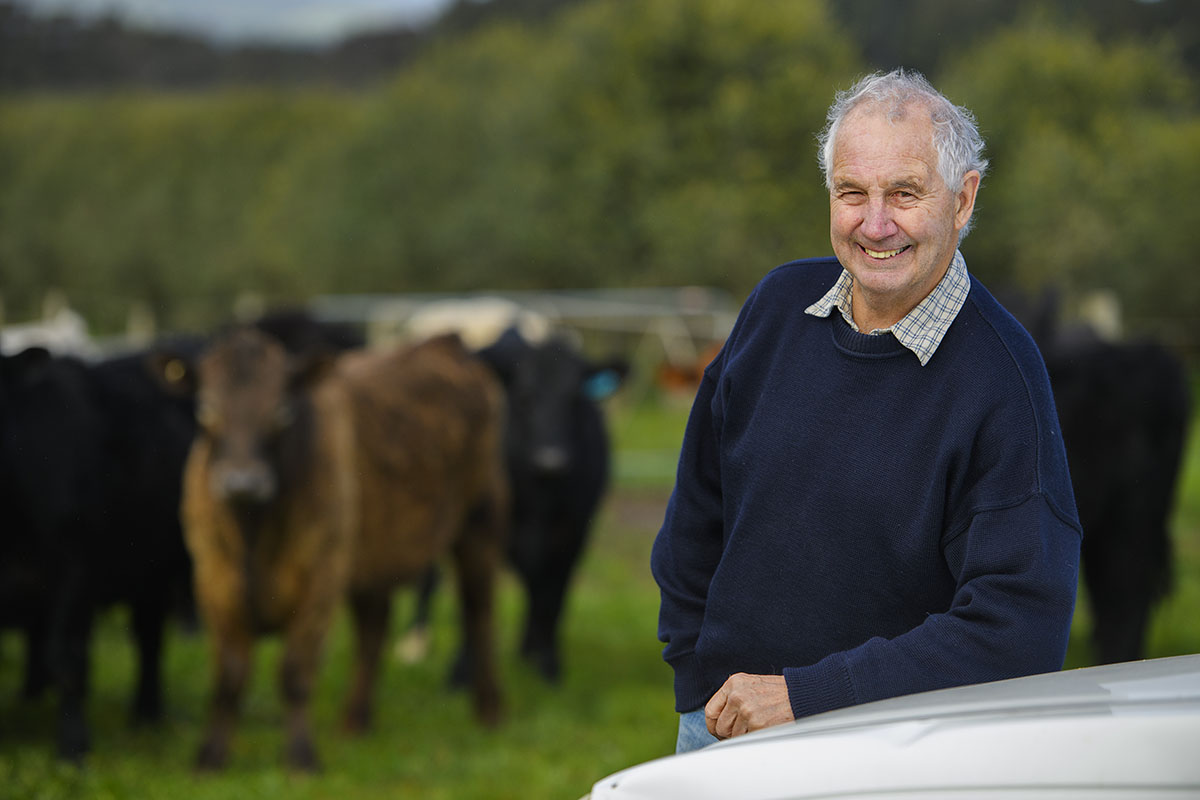
Photos taken by Ben Searcy.
Keep reading more stories
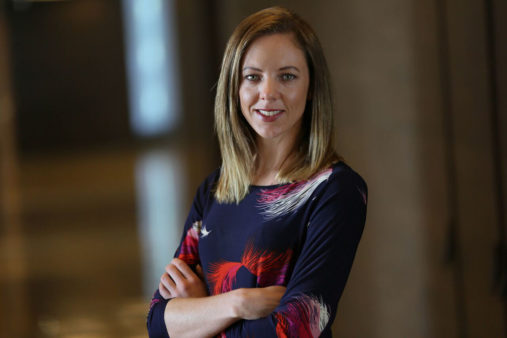
Kate Hage: Bridging the gap
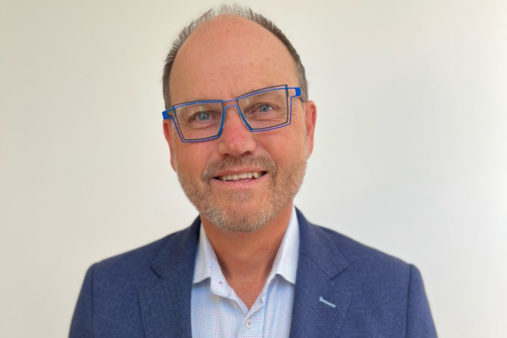
Stephen Shepherd: Empowering co-operatives
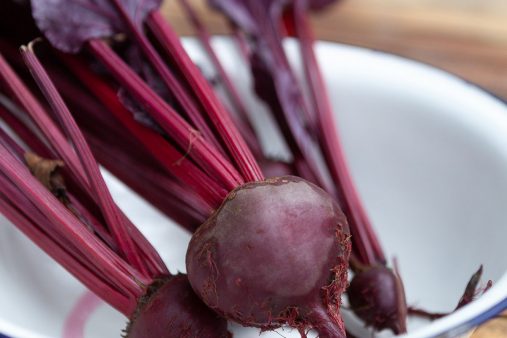